2- روش جذب جامد به وسیله جامدات نمک گیر
در این روش علاوه بر بخار آب ناخالصیهای دیگر نیز توسط مواد جاذب جدا می شوند. مکانیزم جذب به سه طریق انجام میشود.
جذب سطحی
ایجاد اب هیدارته با مواد جامد
واکنش شیمیایی با جامد
روش جذب سطحی بیشترین کاربرد را برای آبگیری در پالایش گاز دارد.
به طور کلی یک ماده جاذب باید دارای خصوصیات زیر باشد:
دارای سطح زیاد بر واحد وزن باشد.
نسبت به اجزاء قابل جذب، فعال باشد.
میزان انتقال جرم در آن زیاد باشد.
احیاء آن آسان بوده و از نظر اقتصادی مقرون به صرفه باشد.
مدت قابل ملاحظه ای مواد جذب شده را در خود نگه دارد.
در مقابل جریان گاز مقاومت کم ایجاد کند.
خرد نشده و به صورت پودر در نیاید.
ارزان، غیر خورنده و غیر سمی باشد. و ترکیب شیمیایی ایجاد نکند.
تغییر حجم قابل ملاحظه در موقع جذب و احیاء ایجاد ننماید.
در اثر مرطوب شدن مقاومت آن کم نشود.
هر گرم از مواد جاذبی که کاربرد صنعتی دارند. سطحی در حدود 500 تا 600 مترمربع ایجاد می کنند. چنین سطحی در صورتی امکان پذیر است. که جسم به علت موئینگی دارای سطح داخلی زیاد باشد. و یا کریستالی در جسم بوجود آید.
متداولترین و مناسب ترین مواد جاذب که در صنعت کاربرد دارند عبارتند از:
بوکسیت (Al2O3) که به طور طبیعی یافت می شود.
آلومینا که عبارت است از Al2O3 فعال شده که بوکسیت تهیه می شود.
سیلیکاژل که قسمت اعظم آن شامل Al2O3 و SiO3 است. به طور طبیعی یافت می شود.
غربالهای مولکولی که شامل سیلیکات کلسیم و سدیم و آلومینیم است.
کربن فعال
در شکل 11-15 سک خشک کن با روش جذب جامد نمایان و معلوم است.
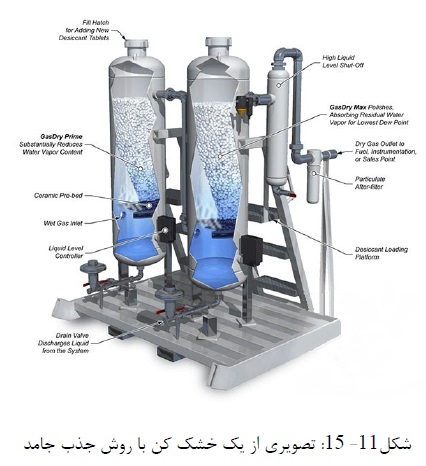
3-میعان بوسیله خشک کردن یا سرد کردن گاز (Refrigeration Compressed Gas Dryer)
در این نوع خشک کن از یک سیل تبریدی برای آب زدایی استفاده می شود.
عملکرد آنها به این صورت است که گاز مرطوب برای خشک شدن. در یک مبدل حرارتی در مجاورت گازی که در یک سیکل تبریدی سرد میشود، قرار می گیرد. بخار آب موجود در گاز با سرد شدن گاز و رسیدن به نقطه شبنم، بصورت قطرات آب تقطیر می شود. هر چه درجه حرارت سرمایش پایین تر آید (تقطیر در دمای پایین تری انجام گیرد)، گاز بیشتر خشک می شود.
انتقال مواد (material handeling)
گاز بعد از سرد شدن وارد یک مخزن جدایش رطوبت می شود. در آنجا آب تقطیر شده جدا می شود.
از گاز خشک خروجی که دارای دمای پایینی است. برای پایین آوردن دمای گاز مرطوب ورودی استفاده می شود. این عمل باعث بالا روی راندمان می شود.
شکل 11-16 اجزاء و چگونگی عملکرد خشکن های تبریدی را نشان می دهد.
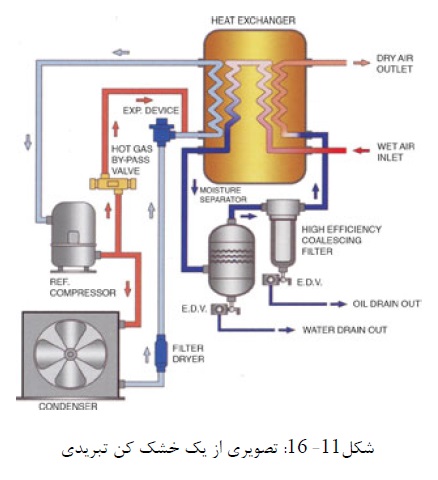
خشک کن هایی که در احیاء مستقیم به روش پرد برای خشک کردن گاز آب بندی (Seal Gas) استفاده می شوند. از نوع جذب در جامد و برای خشک نمودن گاز پاک کننده (Purge Gas) از نوع تبریدی می باشند.
کمپرسورها
کمپرسورها دستگاهی است که برای بالا بردن فشار گاز و یا انتقال آن از نقطه ای به نقطه دیگر. در طول پروسس به کارگیری می شود. در واقع کمپرسور با افزایش سرعت گاز و تبدیل آن به فشار، جریان گاز را در سیستم راحت تر می کند. البته افزایش فشار در نوعی از کمپرسورها به وسیله کاهش حجم صورت می گیرد.
انتقال مواد (material handeling)
آنچه که در کمپرسورها حائز اهمیت است، نسبت فشار خروجی به ورودی کمپرسور می باشد. در کمپرسورها با افزایش فشار، دمای گاز نیز بالا می رود. و این امر باعث ایجاد اختلال در کار قطعات مختلف آن و سیستم روغن کاری می شود.
برای خنک کاری کمپرسورها می شود از یک سیکل بسته سیال سرد (مثل آب) و یا جریان هوا به کار گیری نمود.
همانطور که ذکر شد در کمپرسورها افزایش فشار به دو صورت انجام می گیرد. بر حسب این مورد دو نوع اساسی کمپرسور نیز وجود دارد که عبارتند از:
کمپرسورهای دینامیکی که فشار گاز را با زیاد کردن سرعت آن و سپس، گرفتن سرعت گاز افزایش می دهند.
کمپرسورهای جابجایی مثبت که با کاهش حجم گاز، فشار آن را افزایش می دهند.
البته هر کدام از این کمپرسورها به حسب شکل ساختمانی و نحوه عملکرد، تقسیم بندی می شوند. که در زیر به طور خلاصه بیان میشود.
1- کمپرسورهای دینامیک Compressors Dynamic
سانتریفیوژ Centrifugal Compressor
جریان محوری Axial Flow Compressor
2- کمپرسورهای جابجایی مثبت Positive Displacement Compressor
رفت و برگشتی Reciprocating
دورانی Rotary Compressor
از بین کمپرسورهای نامبرده، کمپرسورهای رفت و برگشتی، سانتریفوژ و جریان محوری بیشتر از سایر کمپرسورها مورد استفاده قرار می گیرند.
کمپرسورهای رفت و برگشتی Recipricating Compressor
این کمپرسورها را می توان به هر اندازه که مورد احتیاج باشد. ساخت در نوع یک مرحله ای آنها، با حرکت رفت پیستون فشار گاز از مکش تا خروجی بالا می رود. اساس کار این کمپرسورها حرکت یک پیستون داخل یک سیلندر است. که با کاهش حجم گاز، فشار آن را بالا می برند.
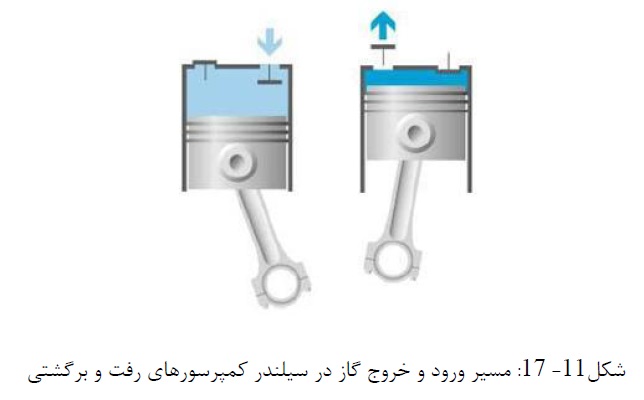
کمپرسورهای رفت و برگشتی یک مرحله ای را بیشتر برای فشار بین 100 تا 150 Psig به کار می برند. از کمپرسورهای دو یا چند مرحله ای زمانی استفاده می شود. که فشار خیلی بالا (مثلاً 100 Psig) مورد احتیاج باشد. اما با توجه به افزایش درجه حرارت گاز به هنگام و حالت متراکم. در کمپرسورهای چند مرحله ای، بعد از هر مرحله از یک خنک کننده استفاده می شود. تا درجه حرارت گاز را برای مرحله بعدی پایین بیاورد. چون حرکت گاز در خروجی این کمپرسورها به طور یکنواخت صورت نمی گیرد. در هر حرکت رفت پیستون، به خروجی کمپرسور ضرباتی وارد می گردد. برای جلوگیر از این ضربات و یکنواخت کردن جریان تدابیر مختلفی به کار می رود که مهمترین انها عبارتند از:
در ضربه ای کردن پیستون، یعنی اینکه پیستون هم در حرکت رفت و هم در حرکت برگشت مقداری گاز متراکم به خروجی مشترکی وارد نماید.
به کار بردن ضربه گیر یا خفه کن: (Pulsation Damper)
ضربه گیر مخزنی است که به طور وارونه در خروجی کمپرسور (اگر چند مرحله ای باشد در خروجی هر مرحله یک ضربه گیر). کار گذاشته می شود. اساس کار ضربه گیر بر پایه انبساط و انقباض گازی که وارد آن میشود استوار است. یعنی اینکه در حرکت رفت پیستون گاز درون ضربه گیر متراکم می شود. و در حرکت برگشت پیستون به علت افت فشار در خروجی کمپرسور. گاز منقبض شده درون ضربه گیر، منبسط شده، از آن خارج شدن وارد لوله خروجی کمپرسور می شود.
مزایای کمپرسورهای رفت و برگشتی:
هنگامی که احتمال تغییر وزن مولکولی گاز ورودی به تأسیسات وجود دارد. از این کمپرسورها استفاده می شود. به این علت که در این کمپرسرها عمل تراکم حساسیت زیادی به وزن مولکول ندارد. این کمپرسورها در مورد گازهای همراه با نفت (Associate Gas)، مناسب می باشند. این کمپرسورها راندمان بالاتری نسبت به کمپرسورهای سانتریفوز دارند. اما دارای سرعت کمتری نسبت به سایر کمپرسورها هستند. لذا بدون احتیاج به جعبه دنده به طور مستقیم می توانند به موتور الکتریکی متصل گردند. برای شروع حرکت نسبت به سایر انواع کمپرسورها توان کمتری لازم دارند. همچنین زمانی که میزان گاز کم باشد. نسبت به انواع دیگر ارجح هستند.
کمپرسورهای سانتریفوژ Centrifugal Compressor
در این کمپرسورها افزایش فشار گاز بر اثر افزایش سرعت آن صورت می گیرد. به این صورت که سرعت گاز بر اثر حرکت پروانه (Impeller) زیاد شده. پس از آن سرعت گاز با برخورد با پخش کننده ها کاهش پیدا می کند. و در عوض فشارش بالا می رود.
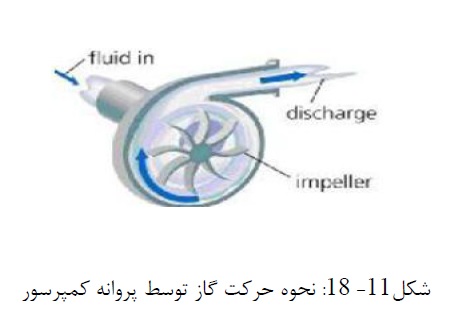
کمپرسورهای سانتریفوژ تشکیل شده اند از یک پروانه که داخل پوسته ای می چرخد. اساس کار این کمپرسورها بر پایه نیروی گریز از مرکز طراحی شده است. در کمپرسورهای سانتریفوژ فاصله بین پوسته و پروانه خیلی کم است. بنابراین جنس محور کمپرسور باید از فلز یا آلیاژی باشد. که در دورهای بالا حداقل انحنا را داشته باشد.
تا پروانه با پوسته تماس پیدا نکند. همچنین گاز ورودی به کمپرسور باید کاملاً خشک باشد. و هیچ مایعی به همراه نداشته باشد. برای همین، قبل از هر کمپرسور یک مخزن آبگیر (Knock Drum Out) قرار می دهند. تا اگر احیاناً قطرات مایعی در گاز موجود است. توسط این مخازن گرفته شود. چون قطرات مایع به پره های کمپرسور ضربه وارد کرده و آسیب می رساند.
اگر فشار خیلی بالا مد نظر باشد. باید از کمپرسورهای سانتریفوژ چند مرحله ای استفاده کرد به خاطر اینکه با افزایش فشار گاز دمای آن نیز زیاد می شود. و این افزایش دما اگر از حد معینی بیشتر شود. باعث آسیب رسانی به قطعات کمپرسور و اختلال در سیستم می شود. همچنین ممکن است با افزایش فشار، قسمتی از گاز تبدیل به مایع شود. و در این قطرات مایع ایجاد میشود و گاز باعث از بین بردن پره های کمپرسور می شود.
به دلایل مورد بیان از کمپرسورهای چند مرحله ای بکارگیری می شود. و به این ترتیب که پس از هر مرحله فشردگی، گاز را خنک کرده و مایع احتمالی در آن را توسط Intercooler. به وسیله مخازنی در بین راه گرفته سپس گاز خشک (بدون مایع) و خشک شده را به مرحله دوم می فرستند. و به این ترتیب می توان پس از چند مرحله فشردن به فشار نسبتاً بالایی دست یافت.
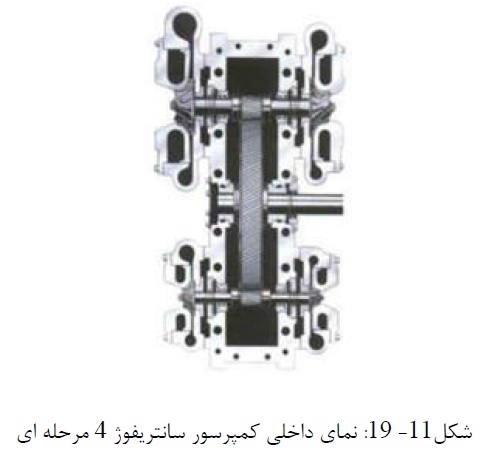
مزایای کمپرسورهای سانتریفوژ
کمپرسورهای سانتریفوژ نیاز به تعمیر کمتری دارند. و می توانند مدت زیادی را بدون وقفه در سیستم کار کنند. علاوه بر آن، این کمپرسورها اندازه کوچکتری نسبت به کمپرسورهای رفت و برگشتی دارند.
زیرسازی کمپرسورهای سانتریفوژ کوچکتر از انواع دیگر است. و نیاز به آب یا روغن خنک کننده ندارد. چون به طور کلی محفظه این نوع کمپرسورها با هوا خنک می شود.
انتقال مواد (material handeling)
جریان خروجی از این نوع کمپرسورها یکنواخت است. و ضربه ای به بخش تخلیه کمپرسور وارد نمی کند. مزیت دیگری که این نوع کمپرسورها دارند این است که استهلاک کمتری نسبت به انواع دیگر دارند. و این به خاطر کم بودن قطعات متحرک این کمپرسور است.
معایب کمپرسورهای سانتریفوژ
کار کرد این کمپرسورها وابستگی شدید به وزن مخصوص، جرم مولکولی و نسبت Cp/Cv گاز ورودی دارد. کاهش وزن مخصوص و وزن مولکولی گاز باعث افزایش توان مصرفی کمپرسور خواهد شد. همچنین متراکم کردن گازهای با وزن مولکولی کم باعث افزایش تعداد مراحل در این کمپرسورها می شود.
با وجود مزایایی که کمپرسورهای سانتریفوژی نسبت به کمپرسورهای رفت و برگشتی دارند، دارای راندمان کمتری نسبت به آنها هستند. موتورهای محرک کمپرسورها به دو صورت الکتریکی و توربینی است. اما با توجه به سرعت زیاد کمپرسورهای سانتریفوژی اگر برای این نوع کمپرسورها از موتورهای الکتریکی استفاده شود.
برای تغییر سرعت دوران برای گازهای متفاوت نیاز به جعبه دنده می باشد. که این امر احتمال لرزش و ارتعاش را بالا می برد. و باعث افزایش هزینه های تعمیرات و استهلاک خواهد شد. در نتیجه کنترل جریان در این کمپرسورها با سهولت کمتری انجام می شود.
کمپرسورهای جریان محوری Axial Flow Compressor
این کمپرسورها نیز مانند کمپرسورهای سانتریفوژ یک قسمت چرخان (Rotor) دارند. که سرعت سیال را بالا می برد. اما بر خلاف کمپرسورهای سانتریفوژ که جریان به صورت شعاعی می باشد. جریان به صورت موازی با محور کمپرسور حرکت می کند. ساختمان این نوع کمپرسورها به صورتی است.
انتقال مواد (material handeling)
که نصف فشار گاز در قسمت جریان (Rotor) و نصف دیگر در قسمت ثابت (Stator) تولید می شود. پره های ثابت شده. بر محور چرخان به ترتیب از قسمت مکش تا خروجی کمپرسور کوچکتر میشود. و باعث بالا رفتن فشار ساکن (Pressure Static) و انرژی جنبشی (Kinetic Energy) گاز می شود. سیستم روغن زنی و سیستم کنترل جریان در سرعت های مختلف در این کمپرسورها دقیقاً شبیه کمپرسورهای سانتریفوژ است.
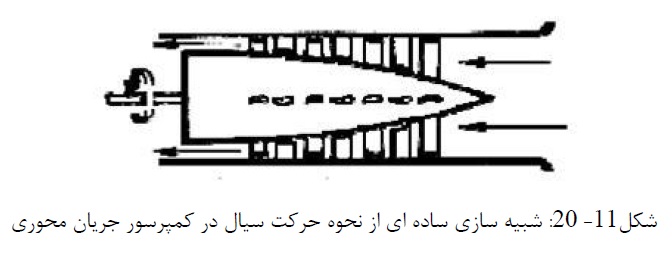
مزایای کمپرسور جریان محوری:
این نوع کمپرسورها اخیراً مصرف صنعتی زیادی پیدا کرده. و برای حجم های خیلی بالا حتی تا 860000 فوت مکعب در دقیقه مناسب ترین کمپرسور می باشد. در مقام مقایسه با کمپرسورهای سانتریفوژ برای فشردگی یک حجم معین گاز قطر چرخان (Rotor) کمپرسور جریان محوری نصف قطر پروانه کمپرسور سانتریفوژ خواهد بود. اگر کمپرسور جریان محوری خوب طراحی و تولید شود. سرعت گاز می تواند ft/s 400 در خروجی برسد.
انتقال مواد (material handeling)
هزینه اولیه تولید یک کمپرسور جریان محوری با هزینه اولیه تولید یک کمپرسور سانتریفوژ برای انجام کار معین برابر است. ولی هزینه نیروی محرکه کمپرسور جریان محوری کمتر از هزینه نیروی محرکه کمپرسور سانتریفوژ می باشد. یعنی اینکه برای یک کار معین، کمپرسور جریان محوری توربین یا موتور برقی کوچکتری نیاز دارد. که این خود باعث کم شدن هزینه های بعدی می گردد.
معایب کمپرسور جریان محوری:
اگرچه این کمپرسورها برای جریانهای بالاتری نسبت به کمپرسورهای سانتریفوژ استفاده می شود. اما ارتفاع ارسال گاز در این کمپرسورها خیلی پایین است. و تقریباً کمتر از نصف کمپرسورهای سانتریفوژ می باشد. که به معنی این است که فشار خروجی در این نوع کمپرسورها خیلی کمتر از کمپرسورهای سانتریفوژ است.
مثلاً برای رسیدن به فشار psig 65 در دوازده مرحله فشرده کردن گاز نیاز است. که این خود باعث افزایش حجم اشغال شده توسط کمپرسور و سایر هزینه ها می شد. با توجه به موارد ذکر شده نتیجه می شود. این کمپرسورها راندمان کمتری نسبت به کمپرسورهای سانتریفوژ دارند.
پمپ ها
پمپ وسیله ای مکانیکی برای انتقال مایعات است. که با افزایش فشار جریان آن، امکان جا به جایی مایعات را به ارتفاعی بالاتر (با افزایش هد). یا حتی پایین دست (معمولاً حوضچه یا مخزن) فراهم می آورد.
به طور کلی پمپ دستگاهی است. که انرژی مکانیکی را از یک منبع خارجی اخذ و به سیال مایعی که از آن عبور می کند، انتقال می دهد. در نتیجه انرژی سیال پس از خروج از این دستگاه (پمپ) افزایش می یابد. از پمپ ها برای انتقال سیال به یک ارتفاع معین. و یا جا به جایی آن در یک سیستم لوله کشی و یا هیدرولیک استفاده می نمایند.
به عبارت کلی تر از پمپ برای انتقال سیال از یک نقطه به نقطه دیگر استفاده می کنند. پمپ ها دارای انواع مختلفی هستند. که هر کدام دارای کاربرد خاصی می باشند. مهم ترین پمپ هایی که مورد استفاده قرار می گیرند عبارتند از:
1- پمپ های سانتریفوژ
2- پمپ های رفت و برگشتی
3- و پمپ های چرخ دنده ای
پمپ های سانتریفوژ
این پمپ ها از نوعی می باشند. که انتقال انرژی از آنها به سیال به طور دائمی انجام می پذیرد. پمپ های سانتریفوژ معمولاً نیروی محرکه خود را از طریق یک الکتروموتور (موتور الکتریکی) دریافت می کنند. انتقال نیروی محرکه از موتور به پمپ از طریق یک محور به نام شفت منتقل می شود. شفت موتور به وسیله نوعی تجهیزات مکانیکی به نام کوپلینگ به شفت پمپ متصل است. به این ترتیب انتقال نیرو به راحتی از طریق شفت موتور الکتریکی به شفت پمپ منتقل می گردد.
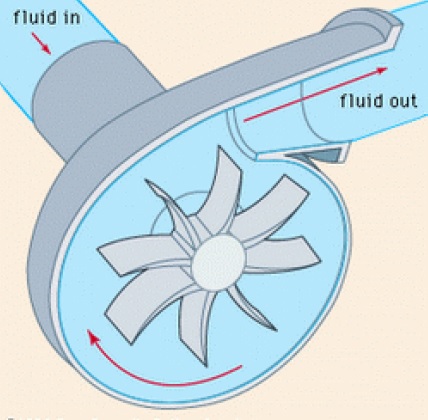
پمپ های سانتریفوژ دارای یک محفظه هستند. که حلزونی شکل است. و پوسته (Casting) معروف است. و درون آن یک یا چند چرخ قرار دارند. که روی یک محور (شفت) نصب شده اند. هر چرخ مجهز به تعدادی پره می باشد. انتقال انرژی به سیال در این قسمت انجام می شود. برای اینکه از محل خروج شفت از کیسینگ پمپ سیالی خارج نشود. و اصطلاحاً نشتی به خارج نداشته باشیم. از ابزاری به نام مکانیکال سیل استفاده شده است. نکته بسیار مهم در مورد این نوع پمپ ها هواگیری یا پرایم کردن پمپ پیش از روشن کردن آنها می باشد. یعنی پس از لاین آب نمدن پمپ اطمینان حاصل نمود. از این نوع پمپ ها در ابعاد و اندازه های مختلف برای مصارف گوناگون تولید می شوند.
پمپ های رفت و برگشتی:
این نوع پمپ ها وسایلی هستند. که انتقال انرژی از آنها به سیال به صورت پریودیک و دوره ای می باشد. نیروی محرکه این نوع پمپ ها نیز غالباً توسط موتورهای الکتریکی تأمین می گردد. در این نوع پمپ ها حرکت چرخشی میل لنگ تبدیل به حرکت رفت و آمدی پیستونی در یک سیلندر می شود.
با عقب رفتن پیستون در سیلندر ایجاد مکش میشود و در نتیجه مایع از طریق یک شیر ورودی داخل سیلندر می گردد. با حرکت پیستون به طرف جلو دریچه ورودی بسته. و مایع از طریق شیر خروجی به خارج هدایت می گردد. شیرهای ورودی و خروجی یک طرفه هستند و طوری تولید میشوند. که در مراحل رفت و آمد پیستون، از ورود مایع داخل سیلندر به قسمت کم فشار و بالعکس ممانعت شود. اگر به جای پیستون، پلانجری در داخل سیلندر رفت و آمد کند.
در این حالت به آن پمپ پلانجری می گویند. در ضمن چنانچه پلانجر دیافراگمی را حرکت دهد. پمپ از نوع دیافراگمی است. فرق میان پیستون و پلانجر در این است که طول سر پیستون کوتاه تر از مسافتی است که پیستون درون سیلندر طی می نمایند. در حالی که طول پلانجر بیشتر از طول مسافتی که طی میشود توسط آن در داخل سیلندر می باشد. از طرفی در پمپ های پیستون از حلقه یا رینگی جهت آب بندی پیستون و سیلندر بکاری گیری میشود. که روی بدنه پیستون قرار میگیرد و همراه آن حرکت می کند.
در حالی که در پمپ های پلانجری این رینگ روی سیلندر قرار دارد، و ثابت است. این پمپ ها معمولاً کم ظرفیت هستند ولی فشار خروجی سیال را می توانند تا مقدار زیادی افزایش دهند. بنابراین از این پمپ ها در جاهایی که. نیاز به جا به جا کردن سیالی با حجم کم ولی فشار بالا می باشد، استفاده می کنند. در ضمن باید به این نکته نیز توجه داشت. که جریان سیال در این پمپ ها به صورت غیر یکنواخت می باشد. نکته بسیار مهم در مورد این پمپ ها آن است. که هرگز نباید آنها را در حالی که شیر خروجی پمپ بسته است روشن نمود.
پمپ های چرخ دنده ای:
این پمپ ها نوعی از پمپ های گردشی یا روتاری می باشند. پمپ های چرخ دنده ای از دو قسمت متمایز تشکیل میشوند. یکی قسمت جداره ثابت و دیگری قسمت دوار که شامل یک محور گردان با چرخ دنده می باشد. در پمپ های چرخ دنده ای مقداری مایع بین دنده های چرخ دنده پمپ به اصطلاح به تله می افتد. و در اثر چرخیدن چرخ دنده ها این مایع به قسمت خروجی پمپ رانده می شود.
این پمپ ها به گونه ای تولید می شوند. که در آنها فاصله میان اجزاء گردنده و جداره ثابت بسیار کم می باشد. کاربرد این پمپ ها برای جا به جایی مایع یا حجم کم و فشار متوسط می باشد. نکته مهم در مورد این پمپ ها آن است که هرگز نباید آنها را در حالی که شیر خروجی پمپ بسته است روشن نمود. چرا که در این حالت، اگر هیچ شیر اطمینانی در مسیر تخلیه پمپ وجود نداشته باشد. یا خود پمپ از بین می رود و یا اینکه لوله تخلیه می شکند.
انتقال مواد (material handeling)
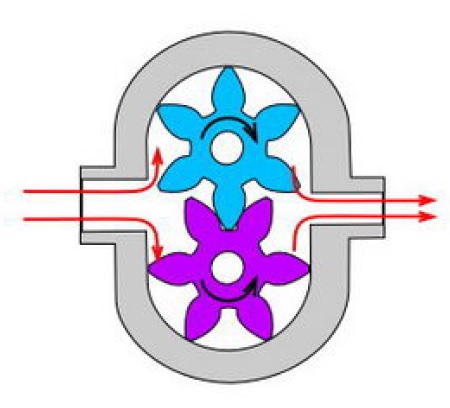
می توان پمپ ها را بر اساس نحوه عملکردشان به گونه ای دیگر نیز دسته بندی کرد:
- پمپ های سانتریفوژ (جریان شعاعی)
- پمپ های محوری
- پمپ های نیمه سانتریفوژ (یا با جریان مختلط)
1- پمپ های سانتریفوژ (شعاعی):
عملکرد این پمپ به این صورت است که در آن سیال موازی محور وارد چرخ پمپ میشود. و عمود بر آن از چرخ خارج می گردد. این پمپ ها معمولاً برای ایجاد فشارهای بالا در دبی های کم به کار می روند. بنابراین اغلب پمپ های سانتریفوژ توانایی خوبی در ایجاد فشارهای بالا دارند. پمپ های سانتریفوژ شایع ترین نمونه از پمپ ها هستند.
2- پمپ های محوری:
سیال موازی محور وارد پمپ می گردد و به طور موازی نسبت به محور از چرخ خارج می گردد. این پمپ ها برای ایجاد فشارها و دبی های متوسط به کار می روند.
3-پمپ های نیمه سانتریفوژ (مختلط):
سیال موازی محور وارد چرخ پمپ می گردد و به طور مایل نسبت به محور از چرخ خارج می گردد. این پمپ ها برای ایجاد فشارها و دبی های متوسط به کار می روند. این پمپ ها نسبت به پمپ های سانتریفوژ توانایی بیشتری در استفاده و به کارگیری دبی های بالا را دارند.
مبانی و کاربرد پمپ های گریز از مرکز (Centrifugal Pump):
اصول کار کلیه این پمپ ها بر اساس استفاده از نیروی “گریز از مرکز” پایه گذاری میشوند. هر حجمی که در یک مسیر دایره ای یا منحنی شکل حرکت کند. تحت تأثیر نیروی گریز از مرکز واقع می شود. جهت نیروی مذکور طوری است. که همواره تمایل دارد که جسم را از محور یا مرکز دوران دور سازد.
قسمت های اساسی یک پمپ گریز از مرکز عبارتند از:
الکتروموتور: که شامل قسمت الکتریکی پمپ است.
کوپل یا هم محور سازی: که متصل کننده الکترومتر به شافت (محور) پمپ است.
انتقال مواد (material handeling)
هوس برینگ: که محل قرارگیری برینگ ها می باشد.
مکانیکال سیل: که محل آب بندی پمپ و جدا کننده سیال پمپاژ میشود و قسمت مکانیکی پمپ می باشد.
پره های پمپ: که با توجه به نوع کاربرد دارای انواع مختلفی می باشد.
مواد:
پمپ های سانتریفیوژ که معمولاً به بازار عرضه می شوند . دارای ترکیبات برنزی، تمام برنزی، یا دارای ترکیب آهنی می باشند. در ساختار نیمه برنزی، پروانه خلاف شافت (اگر به کار برده شده باشد). و رینگ های سایشی برنزی خواد بود. و محفظه از چدن است. این مواد ساختمانی برای قسمت های از پمپ می باشد. که در تماس با پمپاژ شده می باشد.
کاویتاسیون:
این پدیده یکی از خطرناک ترین حالت هایی است. که ممکن است برای یک پمپ به وجود آید. آب یا هر مایع دیگری، در هر درجه حرارتی به ازای فشار معینی تبخیر می شود. هرگاه در حین جریان مایع در داخل یک پمپ، فشار مایع در نقطه ای از فشار تبخیر مایع در درجه حرارت مربوطه کمتر شود. حباب های بخار یا گازی در فاز مایع به وجود می آیند. که به همراه مایع به نقطه ای دیگر با فشار بالاتر حرکت می نمایند. اگر در محل جدید فشار مایع به اندازه کافی زیاد باشد. حباب های بخار در این محل تقطیر میشود و در نتیجه ذراتی از مایع از مسیر اصلی خود منحرف میشود. و با سرعت های فوق العاده زیاد به اطراف و از جمله پره ها برخورد می نمایند. در چنین مکانی نسبت به شدت برخورد، سطح پره ها خورده میشود و متخلخل می گردد.
این پدیده مخرب در پمپ ها را کاویتاسیون می نامند. پدیده کاویتاسیون برای پمپ بسیار خطرناک بوده و ممکن است پس از مدت کوتاهی پره های پمپ را از بین ببرد. بنابراین باید از وجود چنین پدیده ای در پمپ جلوگیری گردد. کاویتاسیون همواره با صداهای منقطع شروع میشود و سپس در صورت ادامه کاهش فشار در دهانه ورودی پمپ، بر شدت این صداها افزوده می گردد. صدای کاویتاسیون مخصوص و مشخص بوده و شبیه برخورد گلوله هایی به یک سطح فلزی است. هم زمان با تولید این صدا پمپ نیز به ارتعاش در می آید. در انتهای این صداهای منقطع به صداهایی شدید و دائم تبدیل می گردد. و در همین حال نیز راندمان پمپ به شدت کاهش می یابد.
دمنده ها (Blowers)
دمنده ها نوع خاصی از کمپرسورها بوده که فشار نسبتاً کم و دبی نسبتاً زیاد دارند. حداکثر فشار قابل دسترس توسط آنها (2-1/5 بار) می باشند. دمنده های با فشار کم و دبی زیاد از نوع گریز از مرکز تولید می شوند. حال آنکه برای فشارهای بالا (نزدیک به 2 بار) و دبی کمتر نوع دورانی (Rorary) متداول تر می باشد. ساخت دمنده های از نوع تناوبی (رفت و برگشتی) عملاً منتفی است.
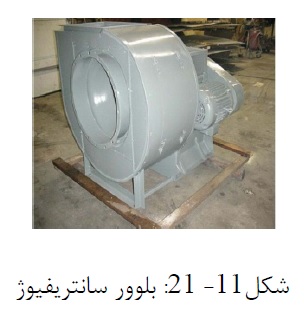
هواکش ها (Fans)
این نوع کمپرسورها عموماً برای دبی زیاد و فشار کم (تا 1-0 بار) ساخته شده و عموماً از خانواده گریز از مرکز می باشند.
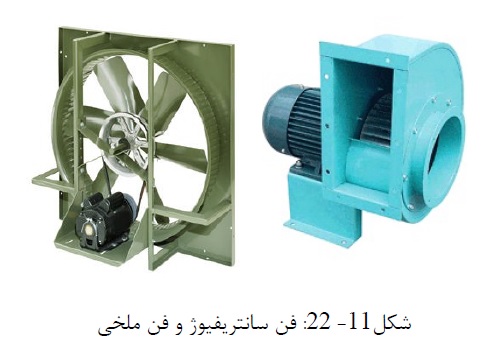
کمپرسورهای اصلی (گاز پروسس و گاز خنک کننده). و همچنین اغلب پمپ ها، بلورها و فن های مورد استفاده در احیاء مستقیم از نوع سانتریفیوژ می باشند.
شرکت خشکه و فولاد پایتخت (( مدیریت : جواد دلاکان )) صنعتگران عزیز، افتخار داریم. که سی سال تجربه گرانبهای خویش را در زمینه عرضه انواع ورق آلیاژی. و انواع فولاد آلیاژی برای خدمت رسانی به شما هموطنان کشور عزیزمان ایران ارائه می دهیم. پیشاپیش از اینکه شرکت خشکه و فولاد پایتخت را جهت خرید خود انتخاب می نمایید سپاسگزاریم.ارتباط با ما:
09121224227
09371901807
تلفن: 02166800251
فکس: 66800546
ارتباط با ما در شبکه های اجتماعی
https://t.me/foolad_paytakht تلگرام
https://www.instagram.com/folad_paytakht اینستاگرام
https://www.instagram.com/foolad_paytakht.ir اینستاگرام