تأثیر عناصر آلیاژی روی فولاد
تأثیر عناصر آلیاژی
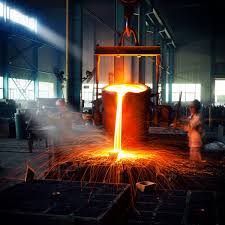
1- کربن (C)
کربن مهمترین و مؤثرترین عنصر آلیاژی در فولادها می باشد. و بالاترین تأثیر را در ساختار آن دارد. هر فولاد آلیاژ شده علاوه بر کربن عناصر آلیاژی دیگری نظیر سیلیسیم، منگنز، فسفر و گوگرد را به همراه خواهد داشت. بطوریکه این عناصر به شکلی ناخواسته به هنگام فرآیند تولید در فولاد باقی خواهد ماند. با افزایش میزان کربن استحکام، سختی پذیری فولاد بیشتر میشود. اما چکش خواری و قابلیت جوشکاری و ماشینکاری (با استفاده از ماشینهای برش) کاهش می یابد. این عنصر عملاً هیچ تأثیری بر مقاومت خوردگی در آب، اسید و گازهای گرم ندارد.
2- کلسیم (Ca)
در ترکیب با سیلیسیم به شکل سیلیسیم – کلسیم در اکسیژن زدایی فولادها به کار می رود. کلسیم، مقاومت در برابر پوسته شدن مواد هادی حرارت را افزایش می دهد.
3- سدیم (Na)
این عنصر یک اکسیژن زدای مسلم و نیرومند است. و گوگرد زدایی را نیز سرعت و شتاب می دهد. به همین دلیل یک عنصر پالایشی در فولادها محسوب می گردد. وجود این عنصر در فولادهای پر آلیاژ باعث گستردگی دامنه فرآیند شکل گیری گرم می شود. همچنین مقاومت فولادهای نسوز را در برابر پوسته شدن بهبود می بخشد. آلیاژهای آهن – سدیم با مقادیر تقریبی 70% سدیم دارای خواص آتش دهندگی (مانند سنگ چخماق) هستند. و در تولید چدنهایی با گرافیت کروی مورد استفاده قرار می گیرد.
4- کبالت (Co)
کبالت هیچ کاربیدی را تشکیل نمی دهد در دمای بالا از رشد دانه ها جلوگیری می کند. مقاومت در برابر تنشهای ناشی از بازپخت را افزایش می دهد. و موجب استحکام مکانیکی فولاد در برابر دمای بالا می شود. لذا به عنوان یک عنصر آلیاژی در فولادهای ابزاری گرم کار و فولادهای مقاوم در برابر خزش و فولادهای دیرگداز به کار می رود. وجود کبالت شکل گیری گرافیت کروی را تسریع می کند. در کمیت ها و مقادیر بالا، پایداری مغناطیسی و نیروی مغناطیسی زدایی و هدایت حرارتی را افزایش می دهد. لذا به عنوان یک عنصر پایه در آلیاژها و فولادهای مغناطیسی دایم مرغوب به کار می رود.
5- کروم (Cr)
وجود عنصر فوق باعث سختی پذیری فولاد در هوا و روغن می باشد. کروم با کاهش سرعت خنک سازی بحرانی به وسیله شکل دادن ساختار مارتنزیتی، قابلیت سخت کاری را افزایش می دهد. بنابراین سبب بهبود حساسیت های سخت کاری و بازپخت می شود. اما در هر صورت چقرمگی کاهش می یابد. و از انعطاف پذیری یا شکل پذیری فولاد به مقدار کمی کاسته می گردد. با افزایش کروم در فولادهای ساده کروم دار جوش پذیری کاهش می یابد. با اضافه نمودن هر واحد (1%) کروم به عنوان یک عنصر کاربید ساز استحکام کششی فولاد. به میزان 100-80 نیوتن بر میلیمتر مربع افزایش می یابد.
کروم به عنوان یک عنصر کاربید ساز بکار برده می شود. کاربیدهای این عنصر کیفیت نگهداری لبه ها و مقاومت سایشی را افزایش می دهد. کروم موجب مقاومت فولاد در دماهای بالا می شود. با افزایش کروم مقاومت در برابر پوسته شدن فولادها نیز بهبود می یابد. به طور تقریبی حداقل 13% کروم مورد نیاز است تا مقاومت خوردگی فولادها نیز بهبود یابد. این عنصر سبب کاهش هدایت الکتریکی و حرارتی می شود. و انبساط حرارتی را نیز کاهش می دهد. با افزایش همزان میزان کربن و کروم تا میزان 3% پایداری مغناطیسی افزایش می یابد.
تأثیر عناصر آلیاژی
6- مس (Cu)
مس به عنوان یک فلز آلیاژی به تعداد بسیار کمی از فولادها اضافه می شود. زیرا این فلز به زیر لایه های سطحی فولاد تمرکز یافته. و در فرآیند شکل دهی گرم با نفوذ به مرز دانه ها، حساسیت سطحی را در فولادها بوجود می آورد. لذا به عنوان یک فلز مخرب در فولادها محسوب می گردد. به واسطه حضور مس نقطه تسلیم و نسبت نقطه تسلیم به استحکام نهایی افزایش می یابد. این عنصر در مقادیر بالای 30% موجب سختی رسوبی می شود. و بدین ترتیب سختی پذیری نیز بهبود می یابد. اما قابلیت جوشکاری به واسطه حضور مس تغییری نمی کند. در فولادهای آلیاژی ساده و پر آلیاژ مقاومت جوی به میزان کافی بهبود می یابد. مقادیر بالاتر از 1% مس موجب بهبود مقاومت در برابر واکنشهای اسید کلریدریک و اسید سولفوریک می شود.
7- هیدروژزن (H)
هیدروژن یک عنصر مخرب در فولاد تلقی می گردد. زیرا بدون آنکه نقطه تسلیم و استحکام کششی فولاد را افزایش دهد موجب تردی و شکنندگی فولاد می گردد. انعطاف پذیری را کم کرده و باعث کاهش سطح مقطع می باشد. هیدروژن سبب پوسته شدن ناخواسته سطح فولاد میگردد. و ایجاد خطوط رنگین ناشی از ترکیبات را شتاب می دهد. هیدروژن اتمی ایجاد شده در خلال فرایند اکسیژن زدایی در فولاد نفوذ کرده و حفره هایی را تشکیل می دهد. هیروژن مرطوب در دمای بالا باعث کربن زدایی فولاد می باشد.
تأثیر عناصر آلیاژی
8- منگنز (Mn)
یک اکسیژن زداست. این عنصر با گوگرد ترکیب شده و تشکیل سولفید منگنز می دهد. بر همین اساس اثرات نامطلوب اکسید آهن را از بین می برد. وجود این عنصر در فولادهای خوش تراش بسیار مهم است. زیر خط قرمز شکنندگی را کاهش می دهد. منگنز سرعت خنک شدن بحرانی را نیز به شدت کم می کند. به همین دلیل سختی پذیری و نقطه تسلیم و استحکام نهایی را افزایش می دهد. با اضافه نمودن منگنز تأثیرات مطلوبی در قابلیت های آهنگری و جوشکاری فولاد بوجود می آید.
و بطور قابل ملاحظه ای عمق سختی فولادها را بیشتر می کند. اگر سطح این نوع فولادها در معرض تنشهای ضربه ای قرار گیرد به مقدار بسیار زیادی کارسخت خواهد شد. در حالیکه مغر فولاد چقرمگی اولیه خود را حفظ میکند. لذا این گروه از فولادها تحت تأثیر نیروهای ضربه ای (کارسختی) مقاومت سایشی مطلوبی از خود نشان می دهند. با افزایش منگنز ضریب انبساط حرارتی افزایش یافته در حالیکه هدایت الکتریکی کاهش می یابد. منگنز باعث افزایش خاصیت فنری می شود.
9- مولیبدن (Mo)
این عنصر به طور معمول با عناصر دیگر آلیاژ می شود. در فولاد کروم-نیکل دار و فولاد منگنز دار سبب ریزدانه سازی می شود. و باعث بهبود قابلیت جوشکاری می شود. و نقطه تسلیم و استحکام نهایی را بالا می برد. با ازدیاد درصد مولیبدن جوش پذیری کاهش می یابد. و سازنده مسلم فاز کاربید است. و در فولادهای تندبر خواص برشکاری را بهبود می بخشد. مولیبدن مقاومت خوردگی را بالا می برد. سختی پذیری را افزایش می دهد. در حدود 0.5- 1.5% مولیبدن به فولادهای آلیاژی اضافه می شود.
تا استحکام و مقاومت خزشی آنها در دماهای بالا حفظ شود. فولادهای زنگ نزن از 0.5 تا 4.0% مولیبدن دارند. فولادهای زنگ نزن آستنیتی برای مقاومت خوردگی بیشتر در محیط های خورنده حاوی مولیبدن مناسب هستند. همچنین، مقاومت در برابر پوسته شدن را می کاهد. عنصر مولیبدن باعث بهبود چقرمگی در فولادهای کربنی ساده با استحکام بالا می شود. و بنابراین در محدوده دمایی قابل استفاده، استحکام و سختی را افزایش می دهد.
در مقایسه با فولادهای کربنی ساده، فولادهای مولیبدن دار خواص الاستیک و استحکام ضربه ای بهتری دارند. با افزودن مولیبدن به فولادهای کم کربنی و مس دار نرخ خوردگی اتمسفری کاسته می شود. با حضور این عنصر، گرافیت زدایی در دماهای بالا کند می شود. مولیبدن، نیتریدهای بسیار مقاوم در برابر سایش در فولاد تشکیل می دهد و بنابراین در فولادهای ابزار نیتریده شونده استفاده می شود.
تأثیر عناصر آلیاژی
10- نیتروژن (N)
این عنصر به دو صورت ظهور می کند
1- بصورت یک عنصر مخرب که به دلیل کاهش چقرمگی در خلال فرآیند ته نشینی، رسوبی است. که موجب ایجاد حساسیت در برابر پیری و شکنندگی (تغییر شکل در درجه حرارت 300-350 درجه سانتی گراد) می شود. و امکان ایجاد تنش در ترکهای درون بلوری فولادهای غیر آلیاژی و کم آلیاژ را فراهم می سازد.
2- بصورت عنصری آلیاژی دامنه فاز گاما را افزایش می دهد. و ساختار آستنیتی را استحکام می بخشد. در فولادهای آستنیتی استحکام را افزایش می دهد و باعث افزایش نقطه تسلیم و خواص مکانیکی در گرما می شود.
11- آلومینیوم (All)
یکی از قوی ترین اکسیژن زداها و نیتروژن زداهاست و بر اساس نتایج به دست آمده. تأثیر بسیار زیادی برای مقابله با کرنش های ناشی از پیری دارد. در ترکیب با نیتروژن تشکیل نیترور می دهد. که باعث افزایش مقاومت در برابر پوست های شدن می شود. به همین دلیل به عناون عنصری آلیاژی برای مقاومت حرارتی فولادها به کار می رود.
12- نیکل (Ni)
این عنصر دو وظیفه مهم انجام می دهد
1- تشکیل و پایدار سازی ساختار آستنیتی، کاهش کار سختی، افزایش شکل پذیری، ایجاد خواص مکانیکی مخصوصاً در دماهای پایین.
2- بهبود خواص خوردگی مخصوصاً در محیط های احیا کننده و اسیدهای معدنی از طریق کمک به تشکیل لایه محافظ.
تأثیر عناصر آلیاژی
نیکل سختی پذیری فولاد را افزایش می دهد. و در حدود 0.25 تا 5 درصد در ترکیب فولاد وجود دارد. نیکل چقرمگی شکست فولاد بهمراه استحکام و سختی آن را افزایش می دهد. در مواقعی که در دماهای پایین به چقرمگی شکست بالا نیاز باشد. در صد آن تا 9 نیز می تواند باشد. و در فولادهای زنگ نزن آستنیتی 7 تا 35 درصد نیکل وجود دارد. در این فولادها برای خنثی کردن از فریت زایی کروم از نیکل بهره می گیرند.
13- سیلیسیم (Si)
سیلیسیم استحکام فولاد را افزایش می دهد. و سختی پذیری را زیاد می کند. همچنین مقاومت سایشی را افزایش می دهد. به علت افزایش استحکام تسلیم، عنصر اصلی در فولادهای فنر است. در مقادیر بالای سیلیس، سختی پذیری و استحکام فولاد افزایش می یابد. ولی این افزایش همراه با کاهش شکل پذیری و انرژی ضربه است. همچنین وجود این عنصر باعث افزایش مقاومت به پوسته شدن در دمای بالا می گردد. ضمناً در محیط های شیمیایی اکسید کننده قوی مانند اسید سولفوریک غلیظ و گرم نیز مقاومت خوردگی را افزایش می دهد.
تأثیر عناصر آلیاژی
14- گوگرد (S)
نقطه تسلیم و مقاومت در برابر کشش فولاد را تغییر نمی دهد. در فولادهای خوش تراش وجود گوگرد عامل مهمی است. در واقع، یکی از راه های افزایش قابلیت ماشینکاری، اضافه کردن گوگرد به ترکیب فولاد است. وقتی ابزار برش روی سطح قطعه کار می کنند. به علت وجود سولفاتت منگنز طول پلیسه ها کوتاه تر می شوند. و نقش روان کار را نیز ایفا می کنند. و در نتیجه صافی سطح بیشتر می شود.
15- فسفر (P)
فسفر خاصیت ماشینکاری، براده برداری، شکنندگی در حالت سرد و استحکام در حالت گرم را افزایش داده. و مقاومت در برابر ضربه را کاهش می دهد.
16- تنگستن (W)
تنگستن کاربرد زیادی در تولید فولاد ابزار داشته و اخیراً در تولید فولادهای پر آلیاژ مقاوم در برابر حرارت نیز استفاده می شوند. سختی پذیری را افزایش می دهد و از افت سختی در دماهای بالا که امری رایج در نوک ابزار است جلوگیری می کند.
در تولید فولادهای ابزار بالأخص فولادهای ابزار تندبر، یکی از عناصر اصلی تنگستن است. در فولادهای تندبر زمینه ای ایجاد می کند که در حین تمپر نرم نمی شود. و کاربید بسیار سخت و مقاوم به سایش می باشند.
17- وانادیوم (V)
با افزودن وانادیم به فولادهای ابزار و آلیاژی سختی پذیری آنها افزایش می یابد. وانادیم به عنوان عنصر آلیاژی در فولادهای کربنی میکروآلیاژی استفاده می شود. و تنها به مقدار کمی کافی است. تاافزایش قابل توجهی در استحکام فولاد به دست آید. وانادیم از درشت شدن دانه های آستنیت جلوگیری می کند. وانادیم، مقاومت به سایش و حفظ دندانه های تیز و استحکام در دماهای بالا را افزایش می دهد. همچنین بخاطر ریز کردن دانه های آستنیتت، قابلیت جوشکاری را بهبود می بخشد.
18- تیتانیوم (Ti)
در فولادهای ضد زنگ نیز برای از بین بردن اثر مخرب کاربید کروم مورد کاربرد قرار می گیرد.
10-نیوبیم (Nb)
در فولادهای ضد زنگ اثری مشابه تیتانیوم را داشته و به تنهایی و یا به همراه تیتانیوم مورد استفاده قرار می گیرد. و در فولادهای آستنیتی، برای بهبود مقاومت خوردگی بین دانه ای و افزایش خواص مکانیکی در دماهای بالا استفاده می شود. در فولادهای مارتنزیتی، نیوبیوم سختی را کم کرده و مقاومت به تمپر را افزایش می دهد. مقدار نیوبیوم مورد نیاز در فولادهای کربنی و کم آلیاژی کم بوده و در حدود 0.05% نیوبیوم. افزایش قابل توجهی در استحکام فولاد را در پی دارد.
20- قلع (Sn)
نقطه تسلیم و مقاومت در برابر کشش فولاد را تغییر نمی دهد. ولی در نورد سرد مشکل زا می باشد. زیرا افزایش این عنصر در فولاد باعث ایجاد ترکیباتی می شود که دمای ذوب آنها پایین می باشد.
21- سرب (Pb)
باعث کم شدن خاصیت نورد در فولاد می شود. کیفیت سطحی فولاد را کم می کند. به دلیل افزایش خاصیت شکل گیری فولاد، در فولادهای اتومات بیشتر مورد استفاده می شود.
شرکت خشکه و فولاد پایتخت (( مدیریت : جواد دلاکان )) صنعتگران عزیز، افتخار داریم. که سی سال تجربه گرانبهای خویش را در زمینه عرضه انواع ورق آلیاژی. و انواع فولاد آلیاژی برای خدمت رسانی به شما هموطنان کشور عزیزمان ایران ارائه می دهیم. پیشاپیش از اینکه شرکت خشکه و فولاد پایتخت را جهت خرید خود انتخاب می نمایید سپاسگزاریم.ارتباط با ما:
09121224227
09371901807
تلفن: 02166800251
فکس: 66800546
ارتباط با ما در شبکه های اجتماعی
https://t.me/foolad_paytakht تلگرام
https://www.instagram.com/folad_paytakht اینستاگرام
https://www.instagram.com/foolad_paytakht.ir اینستاگرام